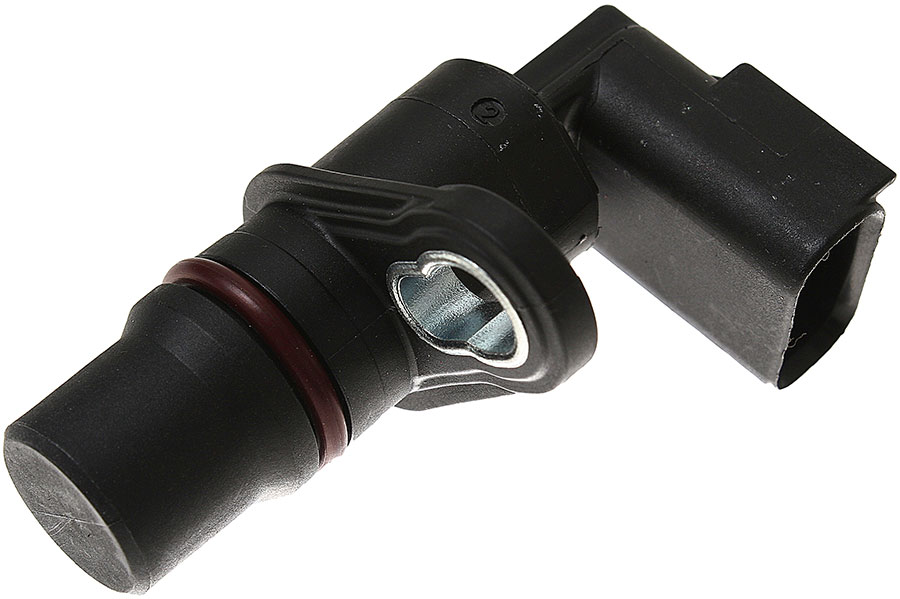
In jedem modernen Aggregat gibt es immer einen Kurbelwellen-Positionssensor, auf dessen Grundlage Zünd- und Kraftstoffeinspritzsysteme aufgebaut sind.Lesen Sie im Artikel alles über Kurbelwellen-Positionssensoren, deren Typen, Aufbau und Funktionsweise sowie die richtige Auswahl und den richtigen Austausch dieser Geräte.
Zweck und Einbauort des Kurbelwellen-Positionssensors im Motor
Kurbelwellenpositionssensor (DPKV, Synchronisationssensor, Referenzstartsensor) – eine Komponente des elektronischen Steuerungssystems des Verbrennungsmotors;Ein Sensor, der die Leistungsmerkmale der Kurbelwelle (Position, Geschwindigkeit) überwacht und die Funktion der Hauptsysteme des Aggregats (Zündung, Leistung, Gasverteilung usw.) sicherstellt.
Moderne Verbrennungsmotoren aller Art sind größtenteils mit elektronischen Steuerungssystemen ausgestattet, die den Betrieb des Aggregats in allen Betriebsarten vollständig übernehmen.Den wichtigsten Platz in solchen Systemen nehmen Sensoren ein – spezielle Geräte, die bestimmte Eigenschaften des Motors verfolgen und Daten an die elektronische Steuereinheit (ECU) übertragen.Einige Sensoren sind für den Betrieb des Aggregats von entscheidender Bedeutung, darunter der Kurbelwellenpositionssensor.
DPKV misst einen Parameter – die Position der Kurbelwelle zu jedem Zeitpunkt.Basierend auf den gewonnenen Daten werden die Drehzahl der Welle und ihre Winkelgeschwindigkeit bestimmt.Durch den Erhalt dieser Informationen löst das Steuergerät eine Vielzahl von Aufgaben:
● Bestimmung des TDC (oder TDC)-Moments der Kolben des ersten und/oder vierten Zylinders;
● Steuerung des Kraftstoffeinspritzsystems – Bestimmung des Einspritzzeitpunkts und der Einspritzdauer der Einspritzdüsen;
● Steuerung des Zündsystems – Bestimmung des Zündzeitpunkts in jedem Zylinder;
● Steuerung des variablen Ventilsteuerungssystems;
● Kontrolle des Betriebs der Komponenten des Kraftstoffdampf-Rückgewinnungssystems;
● Kontrolle und Korrektur des Betriebs anderer motorbezogener Systeme.
Somit stellt DPKV die normale Funktion des Aggregats sicher und bestimmt vollständig den Betrieb seiner beiden Hauptsysteme – Zündung (nur bei Benzinmotoren) und Kraftstoffeinspritzung (bei Einspritzdüsen und Dieselmotoren).Der Sensor erwies sich auch als praktisch für die Steuerung anderer Motorsysteme, deren Betrieb direkt oder indirekt mit der Position und Geschwindigkeit der Welle synchronisiert ist.Ein defekter Sensor kann den Betrieb des Motors völlig stören und muss daher ausgetauscht werden.Bevor Sie jedoch ein neues DPKV kaufen, müssen Sie die Typen dieser Geräte, ihr Design und ihre Funktionsweise verstehen.
Typen, Aufbau und Funktionsprinzip des DPKV
Unabhängig von Typ und Bauart bestehen Kurbelwellen-Positionssensoren aus zwei Teilen:
● Positionssensor;
● Die Master-Festplatte (Sync-Disk, Sync-Disk).
DPKV ist in einem Kunststoff- oder Aluminiumgehäuse untergebracht, das mit einer Halterung neben der Masterplatte montiert wird.Der Sensor verfügt über einen standardmäßigen elektrischen Anschluss zum Anschluss an das elektrische System des Fahrzeugs. Der Anschluss kann sowohl am Sensorgehäuse als auch an einem eigenen Kabel kurzer Länge angebracht werden.Der Sensor wird am Motorblock oder an einer speziellen Halterung befestigt, er befindet sich gegenüber der Hauptscheibe und zählt während des Betriebs seine Zähne.
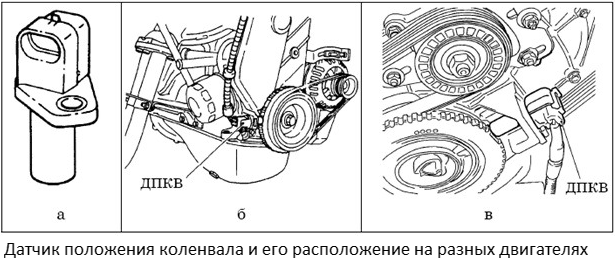
Kurbelwellenpositionssensor bei verschiedenen Motoren
Die Masterscheibe ist eine Riemenscheibe oder ein Rad, an dessen Umfang sich Zähne mit quadratischem Profil befinden.Die Scheibe ist starr an der Kurbelwellenriemenscheibe oder direkt an ihrer Spitze befestigt, wodurch die Drehung beider Teile mit der gleichen Frequenz gewährleistet wird.
Der Betrieb des Sensors kann auf verschiedenen physikalischen Phänomenen und Effekten beruhen, am weitesten verbreitet sind drei Arten von Geräten:
● Induktiv (oder magnetisch);
● Basierend auf dem Hall-Effekt;
● Optisch (leicht).
Jeder Sensortyp hat seine eigenen Konstruktionsmerkmale und Funktionsprinzipien.
Induktiver (magnetischer) DPKV.Das Herzstück des Geräts ist ein Magnetkern, der in einer Wicklung (Spule) untergebracht ist.Die Funktionsweise des Sensors basiert auf der Wirkung elektromagnetischer Induktion.Im Ruhezustand ist das Magnetfeld im Sensor konstant und in seiner Wicklung fließt kein Strom.Wenn der Metallzahn der Masterplatte in der Nähe des Magnetkerns vorbeiläuft, ändert sich das Magnetfeld um den Kern abrupt, was zur Strominduktion in der Wicklung führt.Wenn sich die Scheibe dreht, entsteht am Ausgang des Sensors ein Wechselstrom einer bestimmten Frequenz, aus dem das Steuergerät die Kurbelwellendrehzahl und deren Position ermittelt.
Dies ist das einfachste Sensordesign und wird häufig bei allen Motortypen verwendet.Der Vorteil derartiger Geräte ist der Betrieb ohne Stromversorgung – dadurch ist es möglich, sie mit nur einem Adernpaar direkt an die Steuereinheit anzuschließen.
Hall-Effekt-Sensor.Der Sensor basiert auf einem Effekt, den der amerikanische Physiker Edwin Hall vor fast anderthalb Jahrhunderten entdeckte: Wenn Strom durch zwei gegenüberliegende Seiten einer dünnen Metallplatte fließt, die sich in einem konstanten Magnetfeld befindet, entsteht auf den beiden anderen Seiten Spannung.Moderne Sensoren dieser Art basieren auf speziellen Hall-Chips, die in einem Gehäuse mit Magnetkernen untergebracht sind, und die Masterscheiben dafür verfügen über magnetisierte Zähne.Der Sensor funktioniert einfach: Im Ruhezustand liegt am Ausgang des Sensors eine Nullspannung an, beim Passieren des magnetisierten Zahns erscheint am Ausgang Spannung.Wie im vorherigen Fall entsteht beim Drehen der Masterscheibe am Ausgang des DPKV ein Wechselstrom, der dem Steuergerät zugeführt wird.
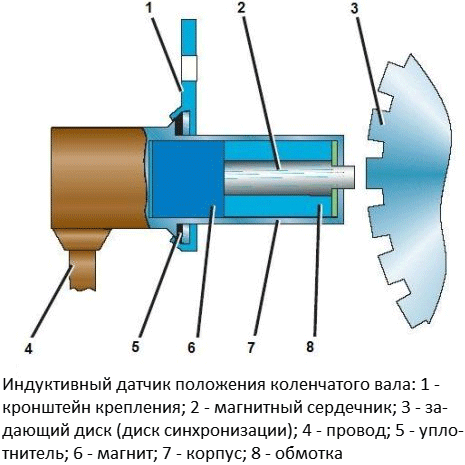
Induktiver Kurbelwellen-Positionssensor
Hierbei handelt es sich um einen komplexeren Sensor, der jedoch über den gesamten Kurbelwellendrehzahlbereich eine hohe Messgenauigkeit bietet.Außerdem benötigt der Hall-Sensor zum Betrieb eine separate Stromversorgung, sodass er mit drei oder vier Drähten angeschlossen wird.
Optische Sensoren.Die Basis des Sensors ist ein Paar Lichtquelle und Empfänger (LED und Fotodiode), in deren Lücke sich Zähne oder Löcher der Masterscheibe befinden.Der Sensor funktioniert einfach: Die Scheibe überstrahlt bei unterschiedlicher Rotation die LED, wodurch am Ausgang der Fotodiode ein gepulster Strom entsteht, der von der Elektronik zur Messung genutzt wird.
Derzeit sind optische Sensoren aufgrund der schwierigen Betriebsbedingungen im Motor – hohe Staubentwicklung, mögliche Rauchentwicklung, Kontamination mit Flüssigkeiten, Straßenschmutz usw. – nur begrenzt einsetzbar.
Für die Arbeit mit Sensoren werden standardisierte Masterplatten verwendet.Eine solche Scheibe ist in 60 Zähne unterteilt, die alle 6 Grad angeordnet sind, während an einer Stelle der Scheibe keine zwei Zähne vorhanden sind (Synchronisationsscheibe Typ 60-2) – dieser Durchgang ist der Beginn der Kurbelwellendrehung und gewährleistet die Synchronisierung des Sensors. Steuergerät und zugehörige Systeme.Normalerweise fällt der erste Zahn nach dem Überspringen mit der Position des Kolbens des ersten oder letzten Zylinders am oberen Totpunkt oder oberen Totpunkt zusammen.Es gibt auch Scheiben mit zwei Zahnsprüngen, die in einem Winkel von 180 Grad zueinander angeordnet sind (Synchronisationsscheibe Typ 60-2-2), solche Scheiben werden bei einigen Arten von Dieselaggregaten verwendet.
Die Geberscheiben für induktive Sensoren bestehen aus Stahl, manchmal gleichzeitig mit der Kurbelwellenriemenscheibe.Scheiben für Hall-Sensoren bestehen häufig aus Kunststoff, in deren Zähnen sich Permanentmagnete befinden.
Zusammenfassend stellen wir fest, dass DPKV häufig sowohl an der Kurbelwelle als auch an der Nockenwelle verwendet wird. Im letzteren Fall dient es dazu, die Position und Geschwindigkeit der Nockenwelle zu überwachen und Anpassungen an der Funktion des Gasverteilungsmechanismus vorzunehmen.
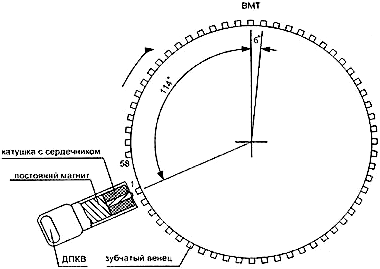
Installation eines induktiven DPKV-Typs und einer Master-Disk
So wählen und ersetzen Sie den Kurbelwellensensor richtig
DPKV spielt eine Schlüsselrolle im Motor, Fehlfunktionen des Sensors führen zu einer starken Verschlechterung des Motorbetriebs (schwieriger Start, instabiler Betrieb, Verschlechterung der Leistungseigenschaften, Detonation usw.).Und in manchen Fällen, wenn das DPKV ausfällt, wird der Motor völlig funktionsunfähig (was durch das Signal „Check Engine“ angezeigt wird).Treten die beschriebenen Probleme mit dem Betrieb des Motors auf, sollten Sie den Kurbelwellensensor überprüfen und bei Fehlfunktion einen Austausch durchführen.
Zuerst müssen Sie den Sensor inspizieren und die Unversehrtheit seines Gehäuses, seines Steckers und seiner Kabel überprüfen.Der induktive Sensor kann mit einem Tester überprüft werden – es reicht aus, den Widerstand der Wicklung zu messen, den der Arbeitssensor im Bereich von 0,6-1,0 kOhm hat.Der Hallsensor kann auf diese Weise nicht überprüft werden, seine Diagnose kann nur an speziellen Geräten durchgeführt werden.Am einfachsten ist es jedoch, einen neuen Sensor einzubauen. Wenn der Motor anspringt, lag das Problem genau an der Fehlfunktion des alten DPKV.
Zum Austausch sollten Sie nur einen Sensor des Typs wählen, der im Auto verbaut war und vom Autohersteller empfohlen wurde.Sensoren eines anderen Modells passen möglicherweise nicht richtig oder machen erhebliche Messfehler und stören dadurch den Betrieb des Motors.Das DPKV sollte gemäß der Fahrzeugreparaturanleitung gewechselt werden.Normalerweise reicht es aus, den elektrischen Stecker zu trennen, ein oder zwei Schrauben/Bolzen herauszudrehen, den Sensor zu entfernen und stattdessen einen neuen zu installieren.Der neue Sensor sollte sich in einem Abstand von 0,5-1,5 mm vom Ende der Masterscheibe befinden (der genaue Abstand ist in der Anleitung angegeben), dieser Abstand kann mit Unterlegscheiben oder auf andere Weise angepasst werden.Mit der richtigen Wahl des DPKV und dessen Austausch beginnt der Motor sofort zu arbeiten, nur in einigen Fällen ist es erforderlich, den Sensor zu kalibrieren und die Fehlercodes zurückzusetzen.
Zeitpunkt der Veröffentlichung: 13. Juli 2023